Pallet Handling Solutions: Reducing Cost per Pallet With High-capacity Material Handling Solutions
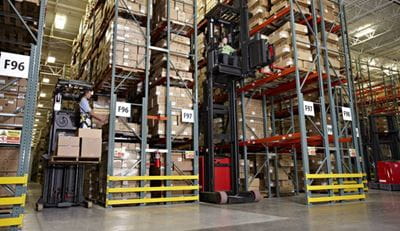
The unprecedented growth in e-commerce has created challenges for warehousing and distribution operations, making it more important than ever to reduce their cost per pallet.
How? In theory, it’s simple: Put more pallets into a given square footage. When building expansions are not viable options, looking up to utilize open space above may offer the best return. Typically, this means either expanding “up” by adding a layer of racking or “in” by creating a very narrow aisle (VNA) layout. Both are valid approaches to creating additional slotting space; but before you take these or any other measures, it pays to make sure your current processes and workflow are doing what you need them to do.
OPTIMIZE CURRENT PROCESSES FOR STORAGE AND E-COMMERCE
If the goal is reducing the cost per pallet stored, changes to the facility infrastructure, along with incorporating equipment with additional capabilities, may well be parts of the solution. A good first step, however, involves optimizing your current processes and workflow for cost minimization by using lean management techniques.
Lean management is based on the idea that continuous incremental improvements in efficiency can make a major impact on overall productivity and profitability. Lean management methods can help you minimize costs by identifying and eliminating waste and inefficiency, reducing lead times, reducing downtime, and improving quality.
A lean management effort starts with visualization — that is, by examining existing processes and facilities with an eye toward gathering as much information as possible about the operation, the workforce, and the workflow.
Next comes the process of identifying and eliminating waste in the operation. Companies bring employees into the effort at this stage by training and empowering them to: identify inefficiencies; pinpoint the value-added and non-value-added steps of the process; and suggest and implement improvements to the tasks they perform daily.
Once you’ve identified value-added and non-value-added steps, you can begin to develop key performance targets and deploy standardized work processes, reducing waste while improving safety, efficiency, and throughput. You’ll also have a better idea of what you might gain by increasing the number of slotting spaces and what equipment might be necessary to help you take advantage of those spaces.
OPTIMIZING SLOTTING AND STORAGE SPACE IN EXISTING FACILITIES
Randomized storage, velocity-based slotting — there are any number of slotting strategies, and they can each be effective depending on the facility, the nature of the stored goods, the equipment fleet, and the labor pool. But the goals of any slotting strategy are the same: maximize available space, remove choke points, maximize labor utilization by reducing travel and picking time, and, ultimately, minimize cost per pallet stored.
For managers of existing facilities, the options for optimizing storage may be limited by the building’s physical dimensions — the ceiling height and square footage. That said, it’s worth questioning which is the real limiting factor: the dimensions of the facility itself or the capabilities of the current equipment fleet. In other words, could slots be added to the current facility if higher-capacity material handling equipment were part of the solution?
High-capacity equipment, for example, can allow operators to reach a full level or more higher than they previously could, meaning you can add another full layer of rack space. High-capacity equipment also can enable randomized storage — a viable strategy for e-commerce or other operations that continuously add and remove SKUs, or ABC storage — meaning slow-moving, heavier items are stored at height, freeing up more accessible slots for high-demand items and reducing travel, restocking and fulfillment times.
In addition, VNA equipment, used either independently of or in addition to high-capacity equipment, may allow owners and operators of existing facilities to create more storage space by reducing the width of the aisles.
DESIGNING NEW FACILITIES FOR LOWEST COST PER PALLET
But for companies considering new warehousing and distribution facilities, the design options for maximizing slotting space are less limited. And if minimizing cost per pallet and cost per square foot are important, there’s definitely a better direction — going up!
Consider an average facility: 80,000 square feet, with 32 feet of clear ceiling height. Assuming six levels of racking, this facility can store 14,784 standard-sized pallets.
But with 50 feet of clear ceiling height and 10 levels of racking, that same number of pallets can be stored in a facility of a little over half that size — 45,000 square feet. That means a smaller overall footprint, potentially lower construction costs, reduced travel time within the facility for personnel and equipment and, ultimately, a lower cost per pallet stored.
CHOOSING THE RIGHT EQUIPMENT …
But facility design is only part of the equation. To take full advantage of available space and minimize the cost per pallet, you’ll need equipment with the right capabilities — lift trucks capable of lifting heavier loads to greater heights, forklifts that can put any pallet anywhere and orderpickers that can reach the highest levels. How does it all work together? Like this:
Again, consider a planned 80,000-square-foot facility. With a 40-foot maximum ceiling height, you’ll have 16,544 pallet slots. Now, add 10 feet to the ceiling; using equipment like the Raymond High Capacity Reach-Fork® truck, you’ll have access to 19,740 available slots. Bring in the Raymond High Capacity Deep-Reach® truck, and you’re reaching up to 24,640 slots and reducing your annual cost per pallet stored by up to 20%.
… AND THE RIGHT PARTNER
Deep-Reach®, Raymond®, and Reach-Fork® are U.S. trademarks of The Raymond Corporation.
-
-
Pallet Handling Solutions: Storage Space Efficiency GuideSaving space is just the beginning. Using our Storage Space Efficiency Guide, you can calculate your own storage requirements and improve efficiency and productivity at your facility.