You May Also Like:
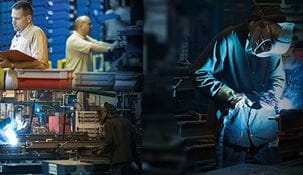
About The Raymond Corporation
Learn more about The Raymond Corporation, a forklift manufacturer, our network of forklift dealers, and our end-to-end material handling solutions.
Learn More
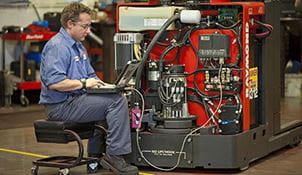
Service and Support Solutions
Our service solutions include maintenance programs, parts, training and asset protection.
Learn More
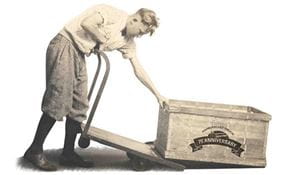
Innovation, Quality and Service
We strive to deliver innovation, quality and service in every customer solution we provide.
Learn More
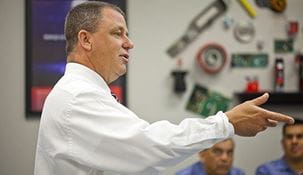
Forklift Operator, Technician and Pedestrian Training
Our award-winning training programs include forklift operator, technician and pedestrian training.
Learn More