Industry 4.0: Refining the Art of Data Utilization
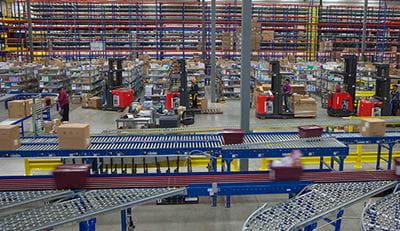
Between all the seemingly disparate systems, applications and processes designed to capture data, it might be easy to forget why we’re collecting it in the first place. Sure, your labor management system tracks time and your warehouse management system collects operational data all while your equipment delivers performance data, but is that it? After all the money, effort and time you’ve devoted to data collection, is that the extent of its value and usefulness? The principles of Industry 4.0 say it’s not.
Real-time Data: The Current State
In today’s warehouses, multitudes of data types — encompassing everything from inventory, equipment performance, energy usage, employee training history and quality control information — are routinely collected. These data points can be acquired through various software platforms, telematics systems and manual inputs that your operation may already be using. However, until now, the challenge has been connecting these siloed pieces of data together to help uncover inefficiencies we could be missing.
For example, maintenance records collected let us know when the tires of a specific lift truck have been replaced more frequently than others. But here’s the catch: We often lack the “why.” Why are those tires wearing out faster? What are the operating conditions this lift truck is being used in? Are operators not inspecting prior to operation? Is it due to an operator’s driving habits? Or is it something else entirely?
When It All Works Together
The foundation of Industry 4.0 advocates for a more holistic examination of our data, so we don’t just understand that something is happening, but we also know to a great extent why it’s happening. When we can analyze and understand our operation to a greater degree, we can use the data — data that we’ve spent significant money, effort and time on to collect — to its fullest potential.
Improved Maintenance:
Take our previous example of tire replacement. With Industry 4.0 principles and a broad spectrum of data collection in place, we can track that these tires need frequent replacement and pinpoint the reasons behind it. In this example, it is due to the routes this lift truck takes. This is determined by combining maintenance cost tracking data with real-time location system (RTLS) tracking data. Knowing this, we can implement targeted maintenance strategies, extending the life span of our equipment and reducing downtime.
Improved Operational Efficiency:
We can use data collected to fine-tune processes, enhance routing and improve resource allocation. Consider an example of a lift truck charging station. Is it being used correctly to optimize opportunity-charging times? With real-time data, we can see exactly when an operator is on a break or at lunch and, if the lift truck has been plugged into the charger during those times, and when a shift ends. This ensures equipment is ready for use by the next shift and avoids unnecessary downtime due to a low battery-state-of-charge.
Improved Cost-efficiency:
When you understand “why” something is happening, you can make informed decisions to lower costs. For example, if there are common congestion areas that slow down your automated trucks, using that data can allow you to optimize facility layouts or route scheduling to improve throughput, increasing your bottom line and ROI on equipment. Whether it’s reducing maintenance expenses, improving energy utilization or optimizing labor and automation resources, data-driven insights lead to a leaner and more profitable operation.
AI for Supply Chain Managers: The Promise of Predictive Analytics
One of the most exciting aspects of Industry 4.0 is predictive analytics. This technology leverages historical data to predict future outcomes. It can answer questions like “If I optimize this aspect of my operation, what happens to the other areas?” Having the answer to that question enables supply chain managers to make informed decisions, such as if they are equipped to take on extra business or determine if their current operation can handle more SKUs.
Predictive maintenance is another game-changer. Instead of replacing parts based solely on a set schedule or usage hours, you can predict when a piece of equipment, like a lift truck hydraulic pump, will need specific maintenance due to several different dynamic factors. Additionally, predictive maintenance ensures that a technician attends to the lift truck only when necessary, rather than following a fixed routine. This approach leads to labor savings, as technicians do not need to inspect the lift truck on a predefined schedule when maintenance is unnecessary, helping to maximize uptime and provide improved productivity.
The First Steps
The journey to Industry 4.0 might seem daunting, but you’re likely already collecting a significant amount of data. You are building that history of current operations for future analytics needs. As you dive deeper into data utilization and analysis, ensure robust cybersecurity measures are in place to protect sensitive information. It’s important to get your IT department engaged and up to date on current data being collected, as IT can help ensure various applications and systems can communicate effectively. Lastly, collaboration with a trusted supplier can streamline data collection and analysis processes, making your transition to Industry 4.0 smoother.