5 Things you can learn from your operators
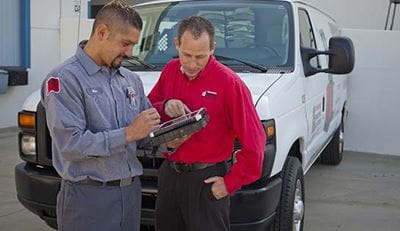
Amid the daily shuffle, many employers may forget to use one of their most valuable resources: employees. It’s important to realize that the people who work around you have insights and opinions that may solve some of your problems. And in the warehouse, your material handling operators want to offer that support by sharing what they think.
Amid the daily shuffle, many employers may forget to use one of their most valuable resources: employees. It’s important to realize that the people who work around you have insights and opinions that may solve some of your problems. And in the warehouse, your material handling operators want to offer that support by sharing what they think.
Operators are the grease in the cogs of a well-oiled warehouse machine. Behind the scenes of many operations, these employees seldom get an opportunity to have their voices heard. We were lucky enough to get some insight into the world of forklift operators, hearing their genuine thoughts on what they want others, and especially management, to know. What they said may surprise you. These are five things your operators wish you knew:
- Don’t take training for granted. Operators have training that allows them to conduct their duties in the right way, blending caution with efficiency. However, when people who are untrained – employees and visitors alike – wander through the warehouse without the caution that training provides, it proves dangerous for them and for the operators. To prevent accidents, brief all who enter a warehouse on the company’s safety procedures.
- Forklift operators aren’t dispensable. They take pride in their work. Operating is not exactly easy. Operators want to be recognized for their skill and have those who fall short be held accountable, even if that means conducting more drug tests or productivity audits. They’ve undergone countless hours of training and certification. Putting someone who has neither in the operator position is disrespectful and dangerous.
- New trucks have a purpose. Operators would rarely turn down a new shiny truck, but splurging has more practical benefits than you might think. New trucks mean updated technology, allowing for better efficiency and higher productivity. They mean more safety features of higher quality. New trucks mean less maintenance and a lower probability of breaking down. In short, they aren’t just shiny new toys.
- Lift trucks and racks don’t always mesh. Operators really don’t like pallets that are hanging over the racks or like having to wait for other trucks to clear an aisle because the racking system isn’t a match for the trucks being used. The rack salesperson and the lift-truck salesperson should be working together to ensure that your warehouse is well-planned out.
- Keep your operators in the light. They don’t need the perfect ambience, but overhead lighting is a must. Broken or damaged lighting should be repaired as soon as possible – grabbing a pallet 30 feet in the air isn’t an easy task in the dark.
These are only a few of the things your operators want you to know. Recognize that you may have untapped resources (like lift truck operators) for improving your business and its day-to-day operations. Talk with them and listen to what they have to say – their answers may surprise you and bring some new and innovative ideas to the forefront.
Submitted on Thu, 08/11/2016 - 12:30
Plant Services, Today's Optimized Facility
Read rel="noopener noreferrer" the original post: https://www.plantservices.com/blogs/todays-optimized-facility/5-things-you-can-learn-from-your-operators/